4167红灯笼主论坛玄机料
—— Changzhou Baide Drying Engineering Co., Ltd ——
- 联系电话
- 0519-8918 6676
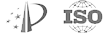
信息来源:本站 | 发布日期: 2019-03-22 17:06:35 | 浏览量:880585
目前,国内绝大多数硅微粉生产厂家采用传统的耙式干燥机烘干硅微粉,由于烘干方式落后,导致生产效率较低,劳动强度较大,环境污染较严重,生产成本较高。而采用盘式连续干燥器干燥硅微粉,则明显降低了生产成本,提高了产品质量,降低了工人的劳动强度,保护了环境。因此盘式连续干燥器在硅微粉等非金属矿的干燥上应用前景很好。
4167红灯笼主论坛玄机料-770772老牌红灯笼玄机料-772770红灯笼论坛王中王-770772红灯笼一肖一码-红灯笼论坛玄机料共关注-979991红灯笼玄机料 真空圆盘干燥机与传统夹套加热(耙式)式干燥机比较,前者加热面积为后者的2.5~5倍,主要加热面积(加热盘)埋在…
盘式干燥机应用于干燥、热解、煅烧、冷却、反应、升华等领域,可广泛适用于化工、医药、农药、食品、饲料、农…
真空盘式干燥机适用于烘干温度要求很低或含溶剂的热敏性物料的干燥,如药品、维生素、生物制品、酶等,既防止…
4167红灯笼主论坛玄机料-770772老牌红灯笼玄机料-772770红灯笼论坛王中王-770772红灯笼一肖一码-红灯笼论坛玄机料共关注-979991红灯笼玄机料 盘式干燥机是一种新颖高效烘干设备,它吸收了传导干燥设备的优点、结构上采用了浮动式铧犁形回转搅拌耙叶,主…
4167红灯笼主论坛玄机料-770772老牌红灯笼玄机料-772770红灯笼论坛王中王-770772红灯笼一肖一码-红灯笼论坛玄机料共关注-979991红灯笼玄机料 上海某集团年产5000T氧化铁黄干燥系统选用桨叶KJG-41+盘式PLG-3000X10的二级组合式干燥机组已是百得干燥的成…
4167红灯笼主论坛玄机料-770772老牌红灯笼玄机料-772770红灯笼论坛王中王-770772红灯笼一肖一码-红灯笼论坛玄机料共关注-979991红灯笼玄机料 国内生产膨胀石墨的厂家采用传统对流干燥工艺,生产效率较低,劳动强度较大,设备占地面积大,生产成本高。百…